PLATFORM
Laundry
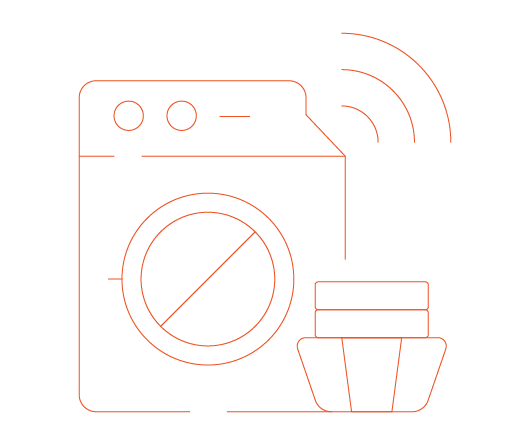
Stock Counter Table
Stock Counter Gate
Stock Distribution Box
SmarTrolley
SmarTractor
Pozi.tech Laundry Management Platform
The platform provides technological support for laundry operations, from a simple local laundry of a hospital to the “Clean textiles as a service” business modelbesed service providers. The Pozi.tech Laundry Management Platform maximizes the tracking and identification opportunities offered by washable RFID tags, in order to increase the operational efficiency of high-volume industrial laundries.
The platform can be implemented for the entire operation of any laundry service provider independently from:
- Number of laundries
- Cleaning technology used in laundries
- Number and location of the issuing and collection points
- Collection logistics systems
- ERP systems
- Nature of the garments and textiles
The components of the Pozi laundry platform can be introduced and applied separately, the individual components can be easily scaled.
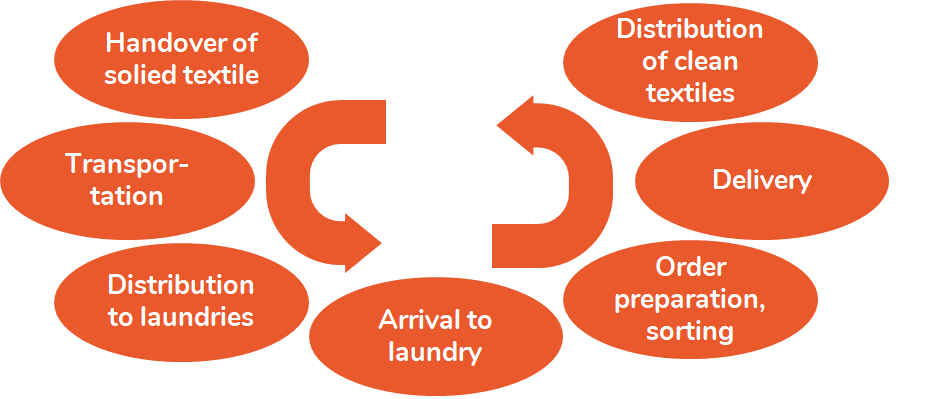
The Pozi.tech Laundry Managment Platform can identify garments and textiles using RFID tags throughout the entire cycle of a laundry operation:
Handover of soiled garments and textiles
With the help of the system, the acceptance of soiled garments and textiles can be automated. The collector cabinet placed at the laundry’s customers automatically identify the item of garments or textile handed over and the receipt is automatically documented.
Transportation
The received garments and textiles can be ordered for storage containers (bags, roll carts, etc.) used during delivery. Containers can be automatically identified in the cargo space during transport. There are no items of garments or textiles lost during transport.
Distribution
In the case of multi-site laundries, the delivery of containers of soiled items can be organized to freights and the planned implementation of the freights can be traced in real time.
Arrival to Laundry
The garments and textiles in the containers delivered to the laundry are individually identified before the washing process begins
Order preparation, sorting
Clean garments and textiles are prepared for delivery on sorting tables. During the compilation of the order, each items prepared in each order is identified. The compilation of orders is automatically documented. The assembled orders are placed in containers, the containers are individually identified and assigned to the given order.
Delivery management
Containers prepared for delivery can be assigned to delivery freights. The assembly of freight cargo is supported by positioning and the pick by light system. The correct composition of the cargo can be checked with the readers placed in the cargo space of vehicles.
Institutional distribution
If the customer of the laundry has an additional distribution task after delivery (eg: sorting of flat textiles to hospital wards), this can be done efficiently with the help of counting tables deployed at clients. The rate of errors during distribution drops to minimum.
Issuing
Dispenser cabinet allows the garments and textiles be automatically issued to end users. The end user identifies himself at the terminal cabinet. After that, the system allows access to those items for which the end user has been granted authorization. The system assigns the removed garments and textiles to the end user without any separate administration
Benefits
The Pozi.tech Laundry Management Platform offers benefits to all parties involved in the operation of a laundry.
Laundry operation
Better order picking accuracy • Better order picking efficiency • Improved capacity utilization • Precise, itemized accounting • Automatic administration
Logistics
Minimized faulty deliveries • Freight planning is simplified • Immediate problem detection and accelerated problem escalation • Additional costs of non-planned operation will be eliminated
Operation outsourced to the client side
Cost-effective issuance and withdrawal • 0-24 hour availability
Financial accounting
Automatic stock register
Stock management
No lost garment or textiles • Possible abuses can be tracked and prevented
Sales, customer relations
Clear, transparent, data-supported settlement with customers • Higher customer satisfaction • Outsourcing service sales and upsales conversion rate improves
Clients
Fast cycle time • Predictable supply • Automatic administration
End users
0-24 hour access • Convenient use • Predictable supply
Platform Components
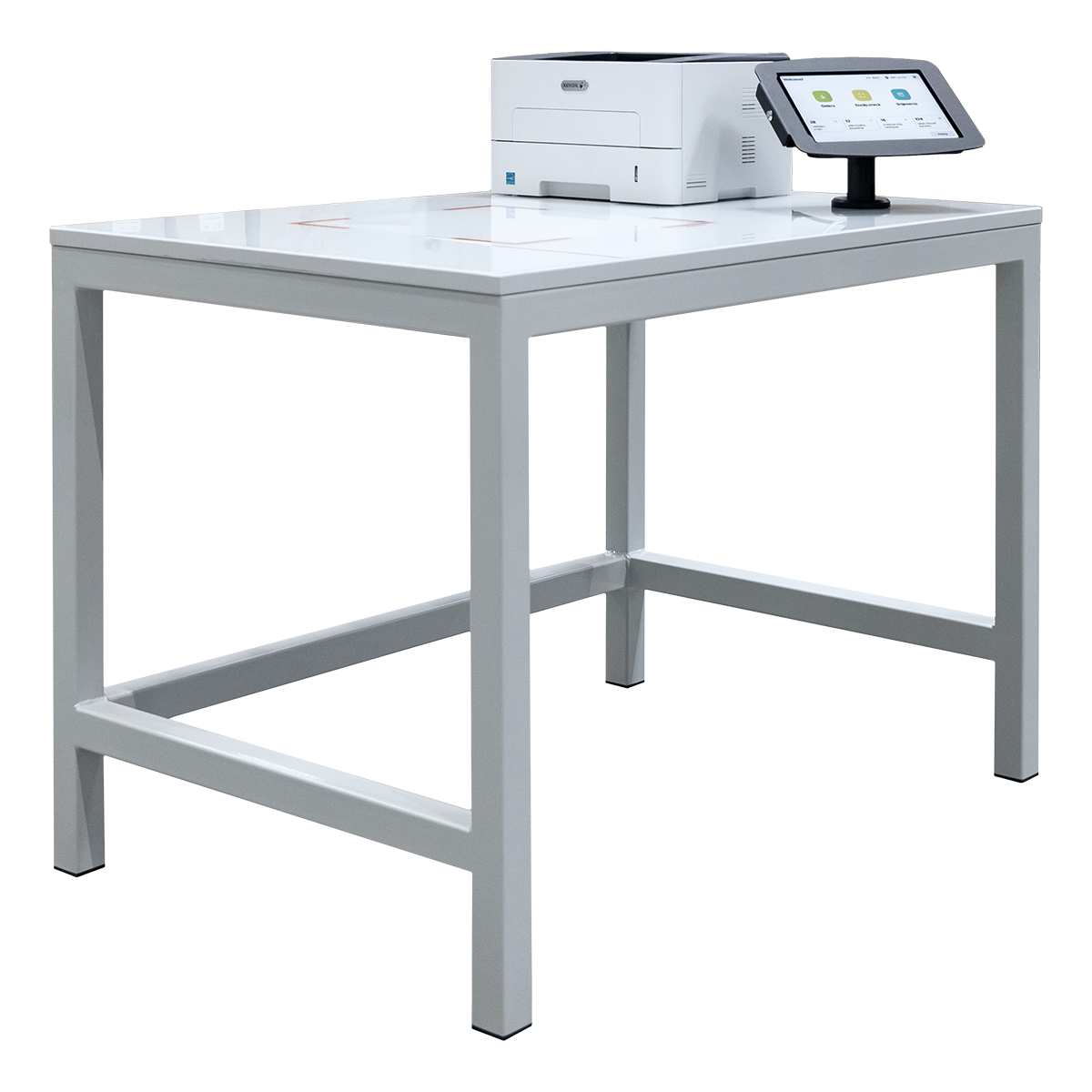
SCT – Stock Counter Table
The module supports the picking and sorting of high-volume, individually RFID identified garments and textiles. The counting table makes available to sort completely or almost identical products and collect orders with high efficiency and reliability. The RFID readers only reads the textiles and garments placed on the table’s reader zone. The administration according to the workflow defined by the customer can be carried out on the built-in terminal. The compiled order documentation can also be attached using the built in printer.
With SCT the incorrect sorting of orders is drastically reduced.
The SCT allows to increase accuracy of identification realy close to 100%.
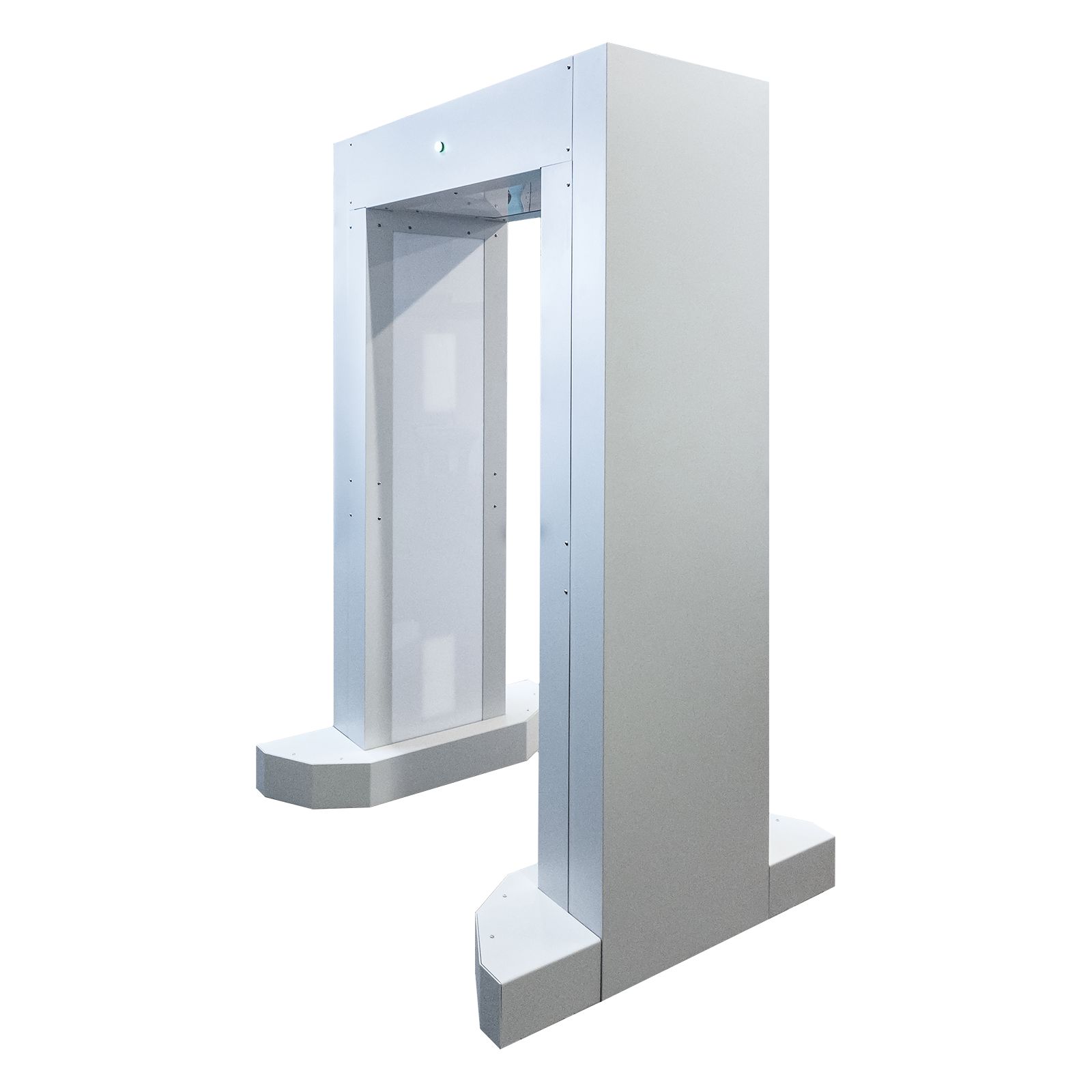
SCG – Stock Counter Gate
The module provide the automatic registration (identification and counting) of high-volume, individually RFID identified packed textiles and garments with RFID gates and readers located at relevant points in the laundry. In the case of a properly installed system, errors resulting from the technological limitations of RFID readings are eliminated and the reading accuracy is 99.9%.
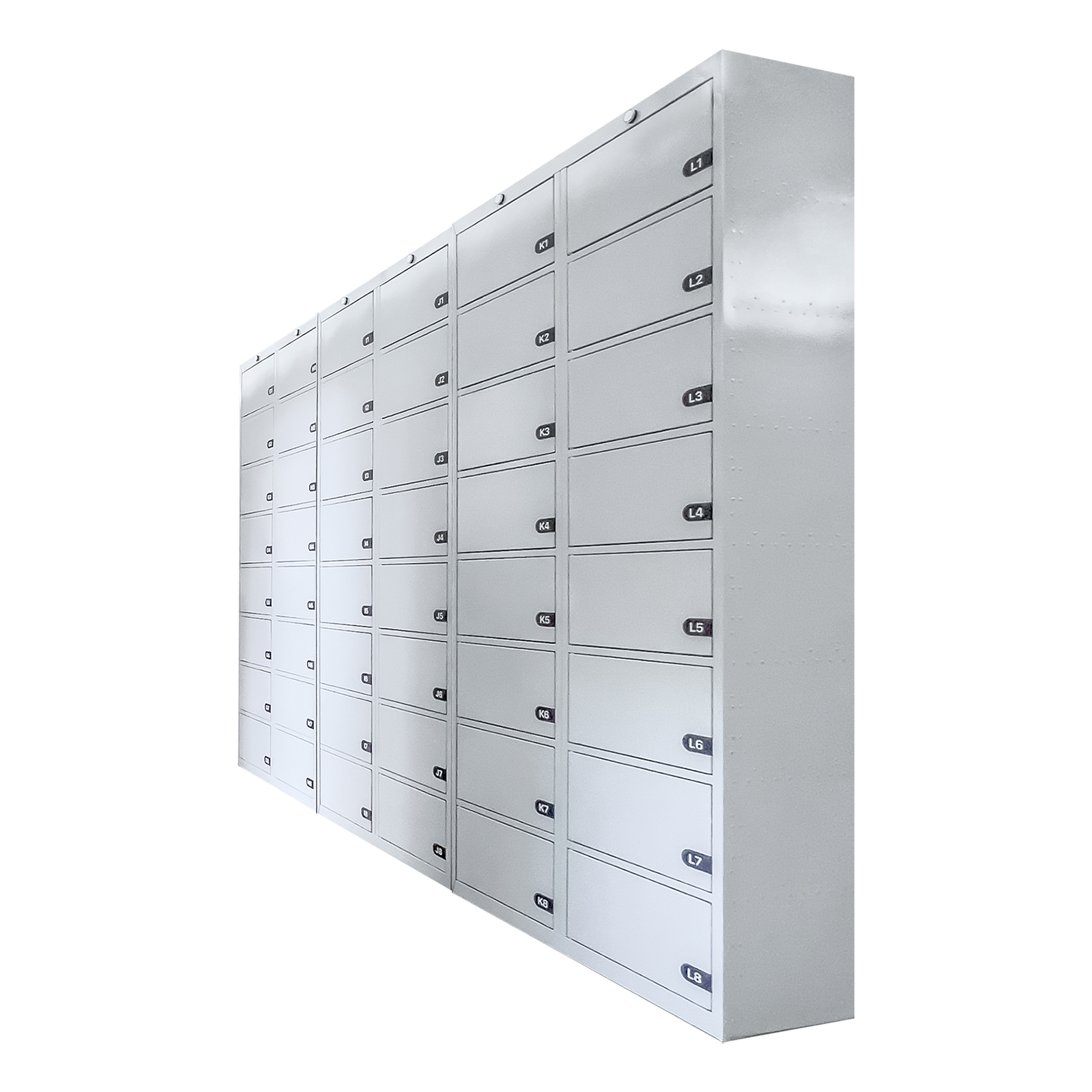
SDB – Stock Distribution Box
The Stock Distribution Box component can be applied independently from other platform components. It provides automated handover of garments and textiles with end-users. It has three main parts:
- Terminal cabinet: This unit contains the elements necessary to implement user interactions, such as the touch screen terminal and the card identification unit as standard equipment. The cabinet can be expanded with additional elements as required (e.g. Printer, QR and Barcode reader, etc.)
- Collector cabinet: This unit is responsible for the automatic collection of garments and textiles. The thrown textiles are readed by the built-in RFID reader. The handover registered automatically in database after the identification of items.
- Dispenser Cabinet: Multi-compartment locker system. Separate RFID antenna is installed in each compartment, so the contents of each compartment can be readed separately. The user can access the compartments with the help of an automatic lock after the identification defined on the terminal unit. The access logic can be freely defined in the system, in the default case the quantity and type of items that can be requested by the given user must be specified in advance. The system only allows access to compartments containing this specified type of content. The items taken out from compartments automatically registered as a handover in database.
In the basic configuration, an SDB module consists of one terminal and collection cabinet and six dispenser cabinets, but these can be freely duplicated and combined.
SDB provide 0-24 access to workware, garments and textiles with documented handover even for thousands of end-users at the same time.
Even hundreds of cabinets can be managed online and real-time in a single distribution system
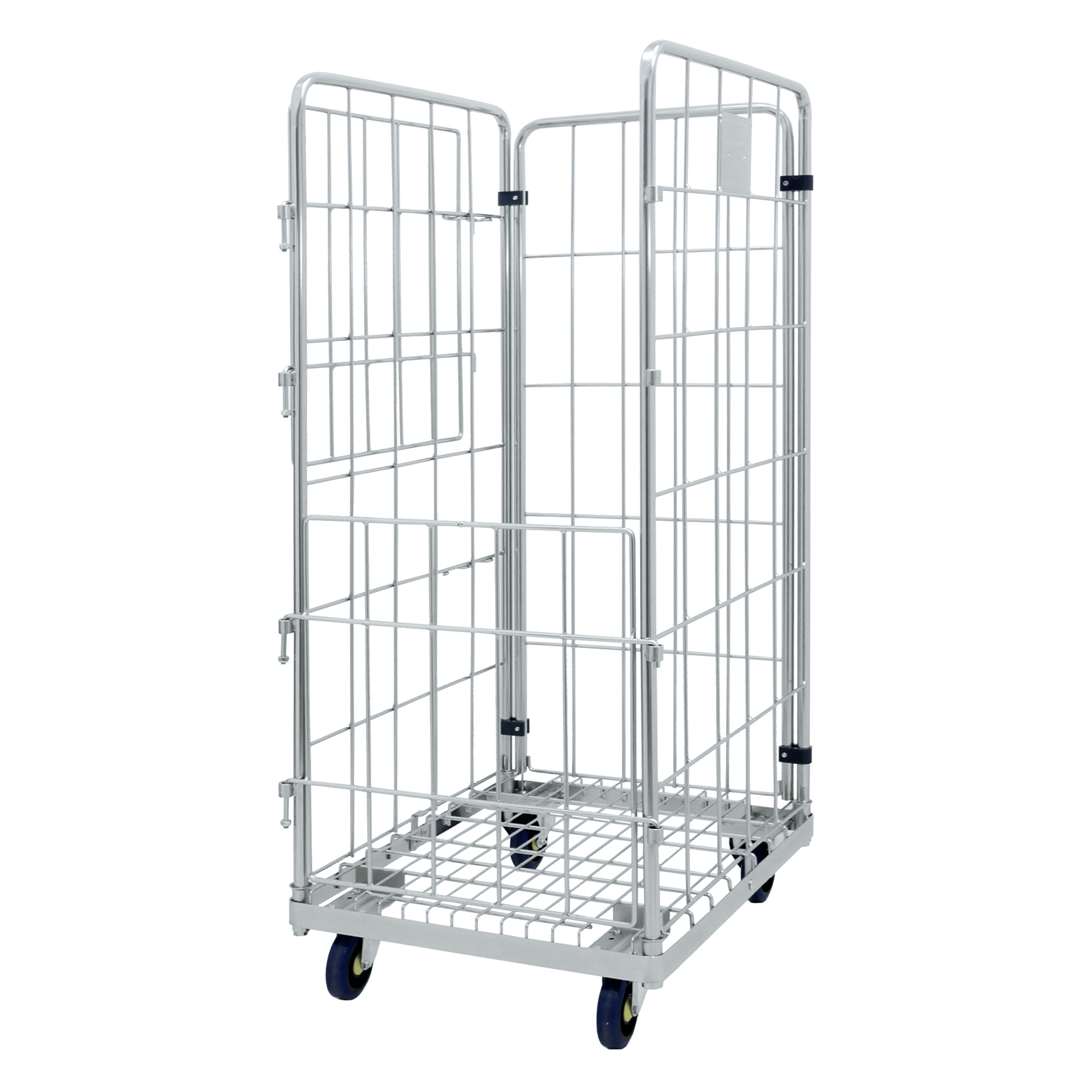
SmarTrolley
The SmarTrolley component offers a solution for tracking roll carts used in laundry logistics. The module design can include positioning, presence detection and identification capabilities according to the desired functions. With the help of remote control sound and light signal, we support the quick finding of the cart you are looking for. The installed hardware can be equipped with different sensors, i. g. sensor for measuring environmental parameters, RFID, Barcode, or QR code reader.
With SmarTrolley laundry can track and trace their roll carts troughout the whole logistics process.
SmarTrolley allows to ensure the accuracy of textile and garments distribution and collection between the laundry and the client.
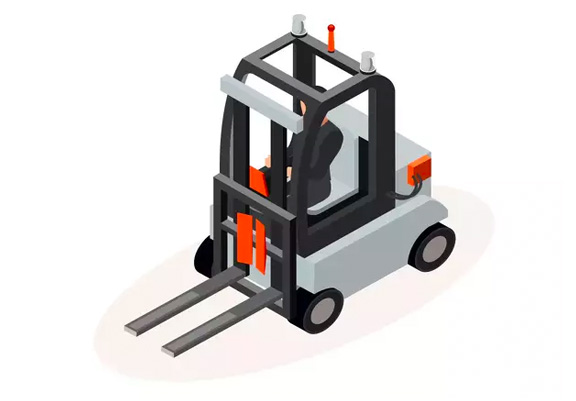
SmarTractor
The SmarTractor component is used to track&trace the delivery and transportation tasks of the laundry operation. Its central unit is a Connect Box with GNSS, 2G/3G/4G and BLE capabilities. Additional elements can be connected to this according to the required functions:
- BLE beacon for car driver identification
- CAN BUS connector for remote reading
- Various other sensors, if required (Ex.: Opening sensor, thermometer, humidity meter, etc.)
The BLE, UWB or RFID reader unit placed in the cargo area, depends on SmarTrolley technology. It is responsible for the identification and presence detection of the trolleys placed in the cargo area.
Software solutions tailored to individual needs can also be connected to the SmarTractor component:
- Freight tracking
- Freight planning
- Route optimization
- Task managemen
Most of the technologies used in the solutions of the Pozi.tech Healthcare Digital Inventory Management and Service Monitoring Platform Laundry Management Platform are the intellectual property of Pozi Technologies.
Related services
Pozi Technologies provides its customers with a wide range of services related to the introduction and operation of Platform functions:
Consulting
Read more
Sponsored Software Development
Read more
Research and Development
Read more