PLATFORM
Warehouse Logistics
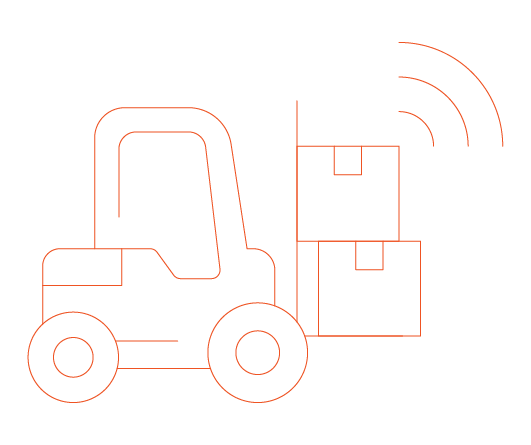
SmarTrace
SmarTruck
SafeTruck
SmarTray
Stock Counter
Table/Gate
Pozi.tech Warehouse Logistics Platform
The Pozi.tech monitoring platform tailored to the needs of warehouse operations. It is a set of compatible, modularly cooperating digital technological solutions. The Platform enables the real-time monitoring of warehouse operation resource usage with detail and content appropriate to current needs.
By deploying a Pozi.tech Warehouse Logistics Platform, together with our customers, we are always looking for effective, customized answers to the actual logistics challenges of a warehouse. The development and maintenance of cost-effectiveness and service quality is a continuous task, but in today’s economic environment, the turn to digital is motivated by new aspects.
Resource utilization
The continuous earthshaking of globalization results that the optimizing of the utilization of existing resources and purchasing of new (or renewed) resources has become a requisite for competitiveness. Only the measurement of resource utilization gives real information for decision on optimization and expansion of resources.
Sustainability
Global climate crisis beside changes in the global energy system mean a new task of optimization and adaptation. Sustainability is based on detailed knowledge of actual resource use.
Adaptability
In the constantly changing economic environment, the ability to quickly adapt becomes a key factor for success. Adaptability is continuously successful change management on the basis of detailed, reliable, tailored to needs, and quickly available information.
Pozi.tech Warehouse Logistics Platform provide reliable, detailed and real-time data on the real functioning of warehouse operations, whether it is resource utilization or current availability, status, or task implementation. In the day-to-day management of the warehouse operation, it is the basic tool for operational data driven decision-making.
The Platform provide a feedback and analysis tool adapted to the current focus areas of operation and process development, which can be used to measure the success of planning tasks with a short response time.
The system is suitable for the simultaneous tracking and for collecting relevant status information of all objects (goods, equipment, human resources) appearing in warehouses. Thanks to its functional and sizing flexibility, the Platform can be successfully used both to manage whole warehouse operations or only individual sub-areas or problem areas.
Pozi giving an integrated answer to the different aspect of warehouse operation challenges:
- all items and articles are automatically tracked, using the technology most suitable for the respective environment
- sophisticated reporting and tracking system gives real-time information on item or vehicle positions
- precisely documents every process, path or movement of the tracked objects, giving valuable data for process planning, quality management and inventory tracking
- provides detailed information on the current state and use of our operational resources
- contributes to the operation safety and compliance with safety rules
Benefits
The Pozi.tech Warehouse Logistics Platform offers benefits to all parties involved in the operation of a warehouse logistics operation in accordance with the expectations of digitization:
Operation Control
Automated registration of uploads and pickings • Efficient picking and picking • Resource availability and utilization monitoring • Process monitoring • Fast problem detection and escalation • Improved KPI
Maintenance & Operations
Real-time resource status information • Resource utilization optimization • Device safety and decreased unplanned maintenance
Process Planning
Radically accelerated design iteration • Real-time feedback for process control • Efficiency measurement • Resource demand feedback • Reality mirror for the digital twin • Norm and cycle time review data
Quality Assurance
Online CTQ monitoring • Documenting production cycle
Environmental Health & Safety
Improved safety conditions • Real-time alerts (Collision & fall detection) • Automated admission of safety rules • Digital documentation of accidents
Sales & Costumer Relations
Realtime progress reports • Transparent proof of performance • More satisfied customers
Finances & Accountancy
Automated and integrated data source of resource performance and allocation • Accurate statistics • Detailed reports
Human Resource Management
Transparent data for performance evaluation • Motivational system review
Platform Components
Pozi platform with combination of data collection components and customization of business software features provide solution for the most diverse needs of our customers.
Each system components can be deployed and used independently, meanwhile the functions and added value offered by each component can be expanded by combining the components.
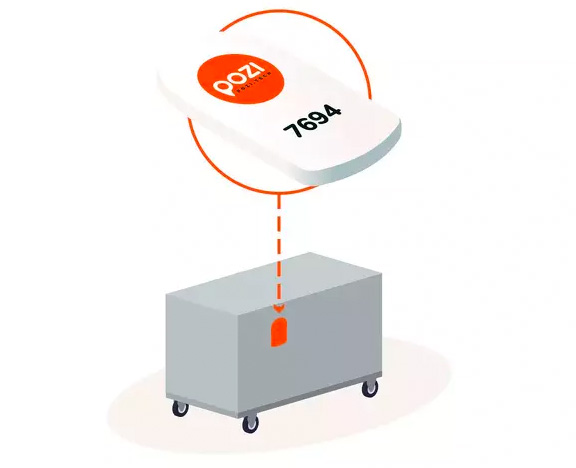
SmarTrace
SmarTrace – the component provides track&trace data – uniquely incorporates all available identification and positioning technologies, along with M2M communication and environmental data.
Pozi’s network and architecture is modular system with a hierarchical topology that supports hybrid infrastructure based on different positioning and measurement technologies.
Pozi’s positioning system built on hard-wired tracker hardware (Anchors) controlled by Sector Masters which then connect to a Gateway. Due to this hierarchical topology the system is highly scalable for even the largest factory floors. Our hard-wired set up divides a warehouse into loops with each loop containing maximum of 64 anchors, covering approx. 1200 m2 or 7.200 m3. Each loop can track up to 5.000 simultaneously moving items. This architecture allows virtually unlimited scaling in terms of covered area, the number of tracked items being in the tens of thousands range.
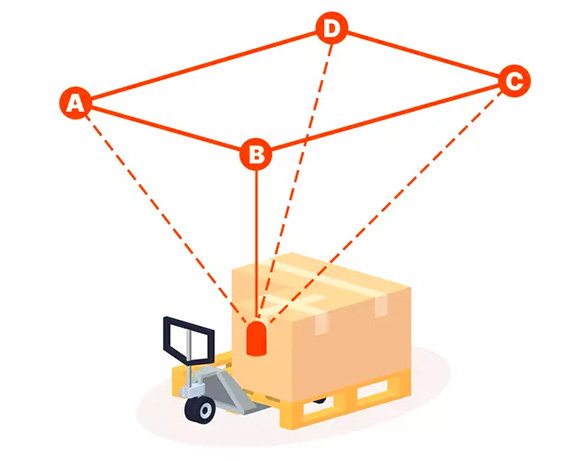
SmarTruck
SmarTruck is the system component for tracking material handling devices as resources. The hardware set that can be installed on a commercial forklift allows full tracking of the devices and the delivered goods. It includes status monitoring, access management, automated device speed limitation. The SmarTruck component also provides functions for RFID-based identification of delivered goods on forklift forks. The SmarTruck software provides full fleet management functionality to the operators of any hybrid fleets.
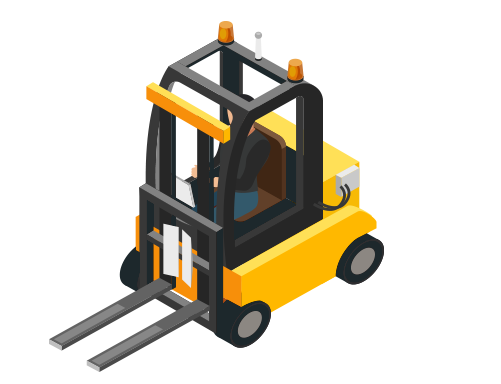
SafeTruck
Safetruck is the autonomous module for EHS protection.
Pozi SafeTruck provides advanced safety features to vehicles involved in production and storage processes: collision prediction and avoidance, speed limitation, automatic emergency braking – while providing safety warnings to workers, pedestrians around.
The module contains a set of hardware installed on forklift, wearable tags for pedestrians, and fixed poles on POIs provide virtual barriers, poles and corridors to mark protected areas.
The modules advanced geospatial software allows complex and dynamic setting of rules that ensure the realization of applied EHS regulations.
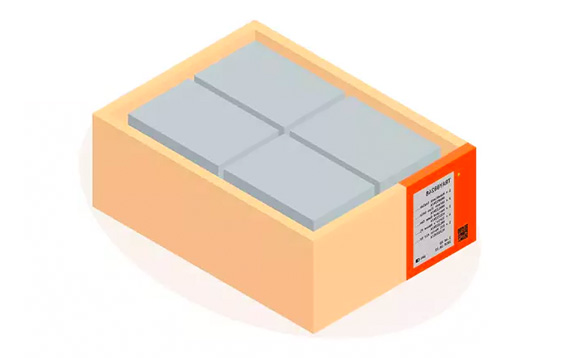
SmarTray
The Pozi SmarTray™ system is a smart storage solution integrating identification and positioning.
SmarTray™ containers provide real-time position and payload data to the Pozi system. Goods or parts are accurately traced without being monitored individually but by following the tray that carries them. The trays includes remote-operated light and sound signaling for pick by light, pick by sound processes and can be optionally set up with additional sensors recording and transmitting payload relevant environmental variables, like temperature, humidity, pressure values, etc.
The general design of trays can be charged standard pallet sized charging station in a rugged and stable construction holds up to 48 trays in a stack. The charging goes cablefree as the lower trays connect the overhead one to the station. SmarTray can be customized to the packaging systems applied by costumer.
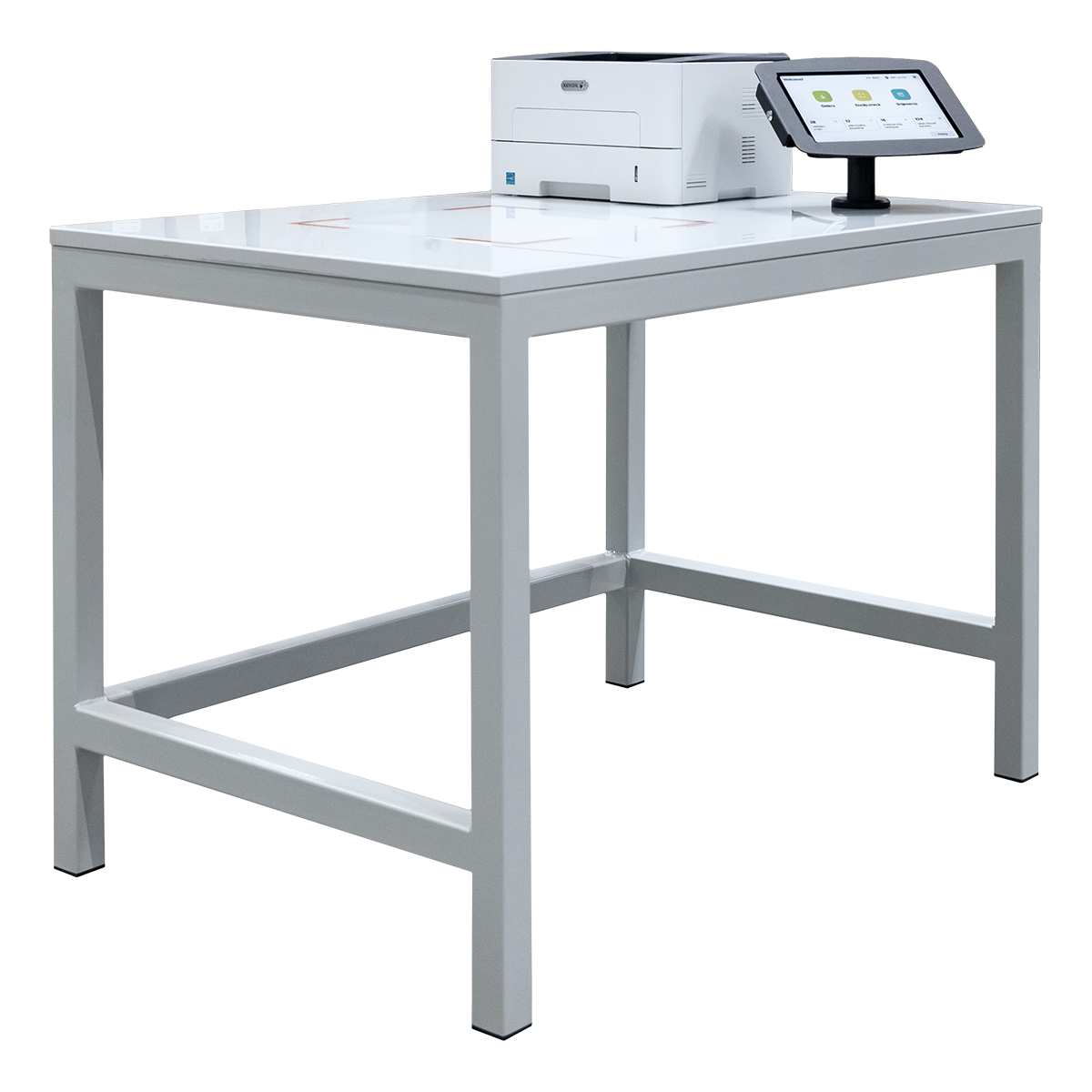
SCT – Stock Counter Table
The module supports the picking and sorting of high-volume, individually RFID identified products. The counting table makes available to sort efficiently completely or almost identical product and collect orders with high efficiency and reliability. The RFID readers only reads the products placed on the table, and the administration according to the workflow defined by the customer can be carried out on the built-in terminal. The compiled order documentation can also be attached using the built in printer. With SCT the incorrect sorting of orders is drastically reduced.
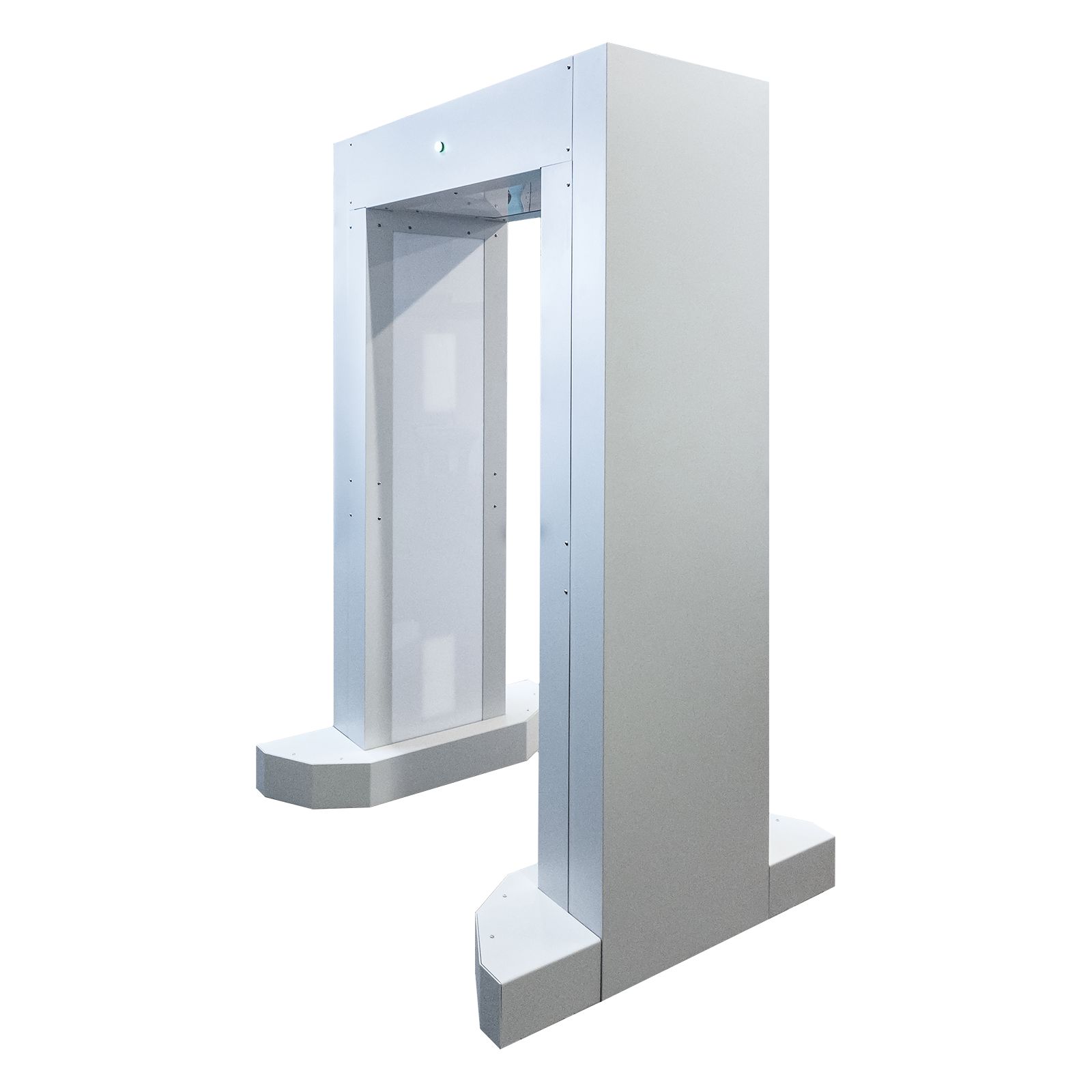
SCG – Stock Counter Gate
The module provide the automatic registration (identification and counting) of high-volume, individually RFID identified products with RFID gates and readers located at relevant points in the warehouses. In the case of a properly installed system, errors resulting from the technological limitations of RFID readings are eliminated and the reading accuracy is 99.9%.
Most of the technologies used in the solutions of the Pozi Production Logistics Platform are the intellectual property of Pozi Technologies.
Related services
Pozi Technologies provides its customers with a wide range of services related to the introduction and operation of Platform functions:
Consulting
Read more
Sponsored Software Development
Read more
Research and Development
Read more